What is Porosity in Welding: Best Practices for Avoiding Porous Welds
What is Porosity in Welding: Best Practices for Avoiding Porous Welds
Blog Article
The Science Behind Porosity: A Comprehensive Guide for Welders and Fabricators
Comprehending the complex devices behind porosity in welding is crucial for welders and fabricators striving for remarkable craftsmanship. As metalworkers look into the depths of this phenomenon, they uncover a world governed by various factors that affect the development of these tiny gaps within welds. From the make-up of the base products to the complexities of the welding procedure itself, a wide variety of variables conspire to either exacerbate or minimize the presence of porosity. In this extensive guide, we will certainly untangle the scientific research behind porosity, exploring its effects on weld quality and introduction progressed methods for its control. Join us on this journey through the microcosm of welding blemishes, where accuracy satisfies understanding in the pursuit of remarkable welds.
Comprehending Porosity in Welding
FIRST SENTENCE:
Evaluation of porosity in welding discloses important understandings into the stability and top quality of the weld joint. Porosity, characterized by the existence of cavities or spaces within the weld steel, is an usual issue in welding procedures. These gaps, if not correctly resolved, can compromise the structural integrity and mechanical homes of the weld, bring about potential failures in the completed item.
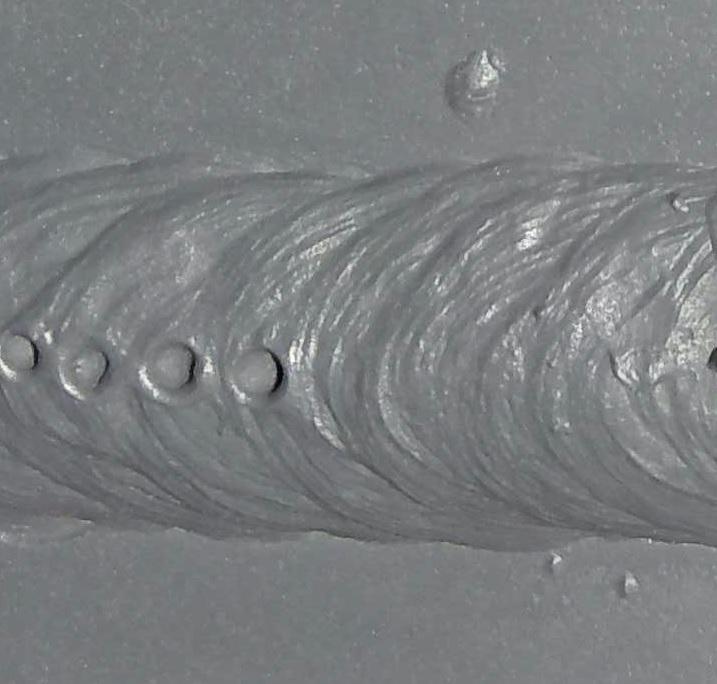
To discover and measure porosity, non-destructive testing methods such as ultrasonic screening or X-ray examination are usually used. These methods permit the identification of inner flaws without endangering the stability of the weld. By examining the size, shape, and distribution of porosity within a weld, welders can make educated choices to improve their welding procedures and accomplish sounder weld joints.
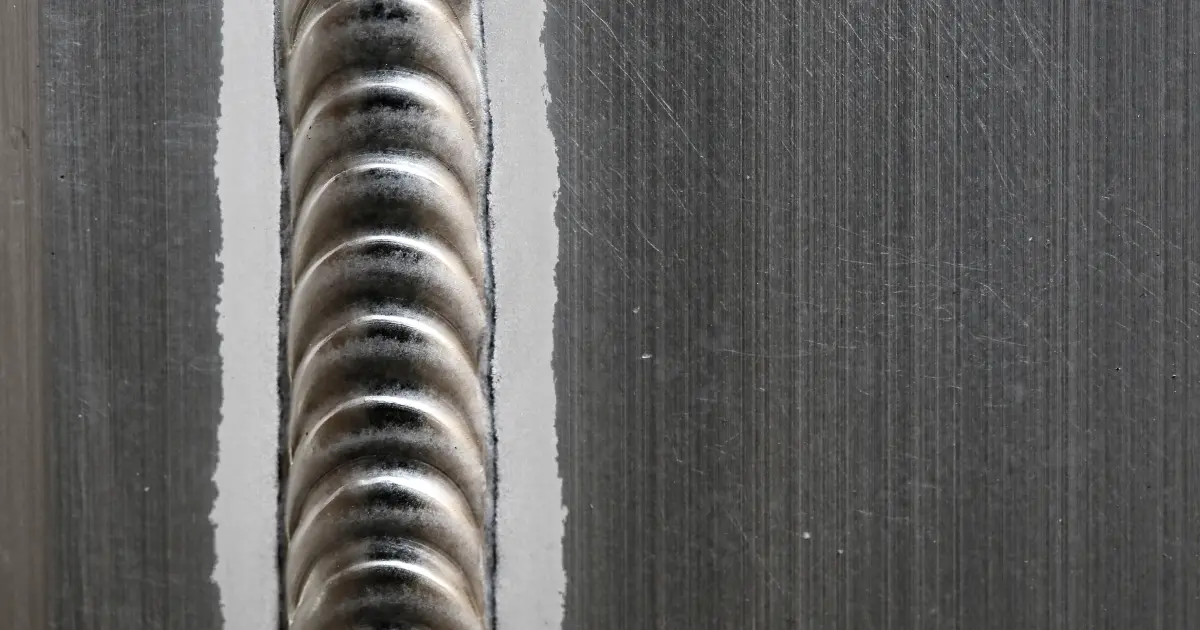
Factors Affecting Porosity Formation
The event of porosity in welding is affected by a myriad of variables, varying from gas securing performance to the details of welding parameter settings. Welding parameters, consisting of voltage, existing, take a trip rate, and electrode kind, likewise effect porosity formation. The welding technique employed, such as gas steel arc welding (GMAW) or secured steel arc welding (SMAW), can affect porosity development due to variations in warm circulation and gas insurance coverage - What is Porosity.
Effects of Porosity on Weld High Quality
The existence of porosity likewise compromises the weld's resistance to corrosion, as the entraped air or gases within the gaps can react with the surrounding setting, leading to destruction over time. Furthermore, porosity can hinder the weld's capacity to stand up to pressure or influence, further threatening the overall top quality and integrity of the welded structure. In important applications such as aerospace, automobile, or architectural buildings, where safety and security and longevity are critical, the destructive effects of porosity on weld high quality can have extreme consequences, highlighting the significance of decreasing porosity through proper welding techniques and procedures.
Methods to Reduce Porosity
Furthermore, utilizing the suitable click for source welding criteria, such as the right voltage, existing, and travel rate, is vital in avoiding porosity. Preserving a regular arc length and angle throughout welding also aids decrease the chance of porosity.

Using the appropriate welding strategy, such as back-stepping or using a weaving motion, can likewise assist disperse warm evenly and lower the chances of porosity formation. By carrying out these techniques, welders can efficiently lessen porosity and generate premium bonded joints.

Advanced Solutions for Porosity Control
Executing advanced innovations and cutting-edge approaches plays a critical duty in achieving remarkable control you could try this out over porosity in welding procedures. One advanced remedy is the usage of innovative gas combinations. Shielding gases like helium or a blend of argon and hydrogen can assist decrease porosity by giving much better arc security and improved gas protection. In addition, utilizing sophisticated welding methods such as pulsed MIG welding or customized environment welding can additionally aid reduce porosity concerns.
One more sophisticated service involves the use of advanced welding devices. Utilizing equipment with integrated functions like waveform control and advanced power resources can boost weld high quality and decrease porosity dangers. In addition, the application of automated welding systems with precise control over specifications can significantly reduce porosity flaws.
Additionally, including sophisticated tracking and assessment innovations such as real-time X-ray imaging or automated ultrasonic screening can click assist in identifying porosity early in the welding procedure, permitting prompt restorative activities. In general, incorporating these advanced options can considerably boost porosity control and boost the overall top quality of bonded parts.
Verdict
In conclusion, understanding the scientific research behind porosity in welding is necessary for welders and fabricators to produce high-grade welds - What is Porosity. Advanced solutions for porosity control can additionally improve the welding procedure and ensure a strong and dependable weld.
Report this page